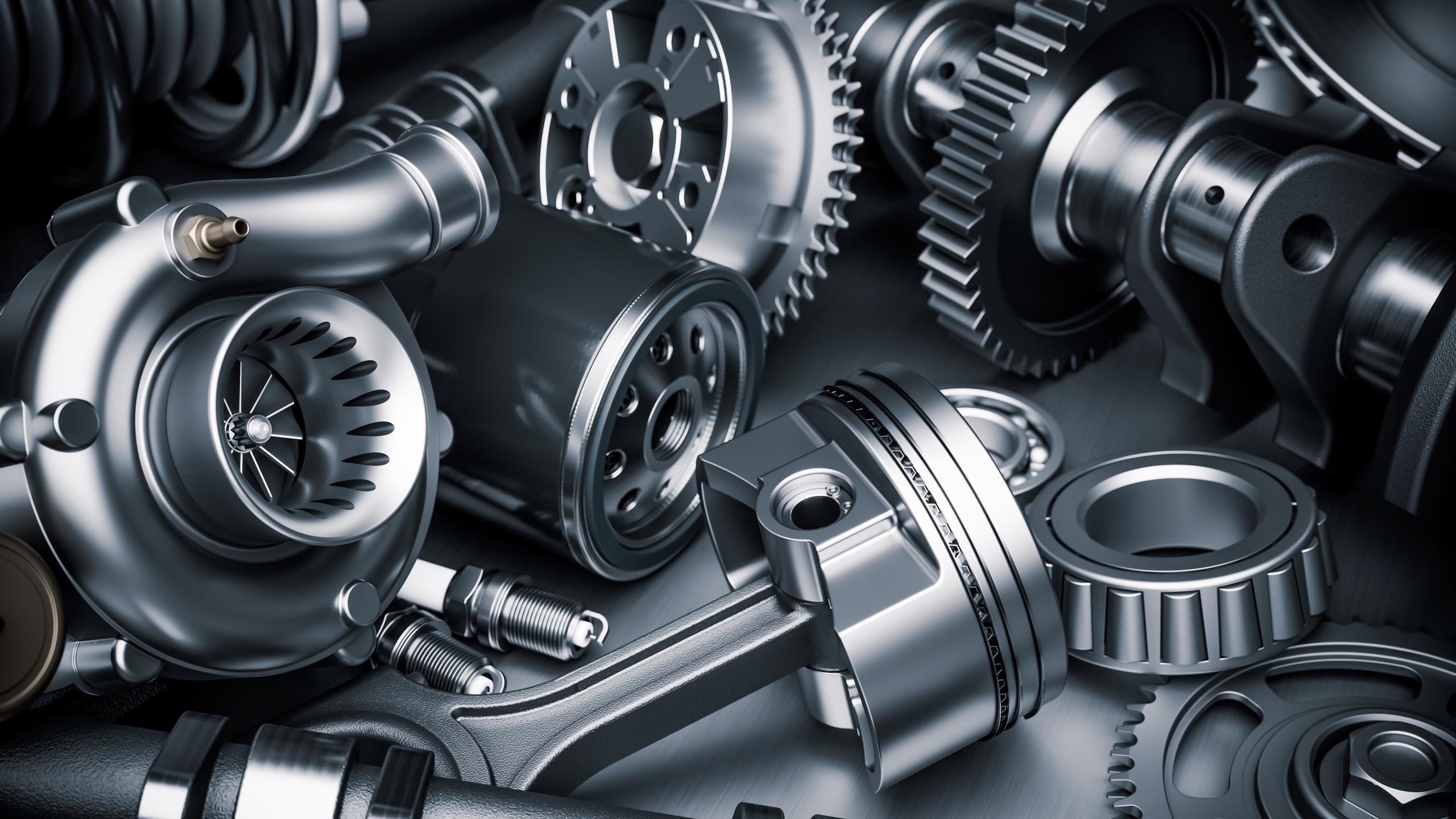
Unipart's digital approach to automotive part traceability
2nd May 2024 | 3 min read
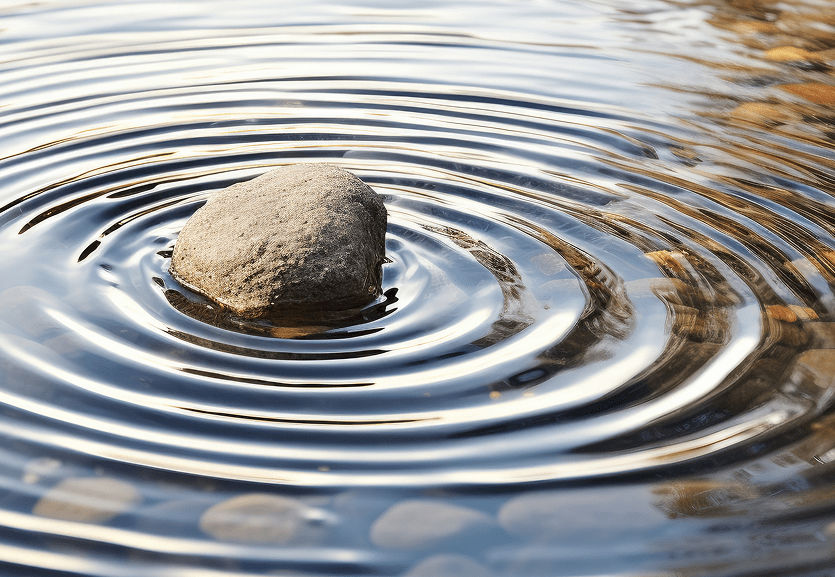
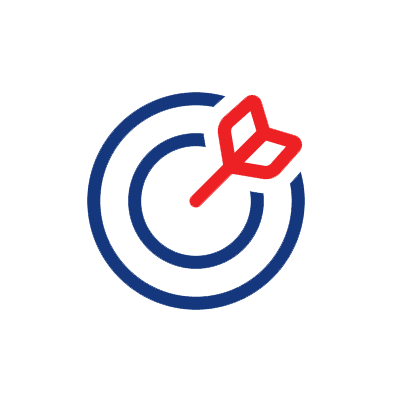
The Challenge
With the complexities of modern manufacturing, every component holds immense importance. Meaning even the most minor oversight can cascade into significant disruptions. Imagine a scenario where the absence of a serial number on a automotive triggers a domino effect of delays, increased costs, and customer dissatisfaction.
Traceability is vital in the Automotive industry as it ensures the quality and safety of parts with defect reduction and recall management1. The close monitoring and documenting of each aspect of vehicle manufacturing and assembly processes can also enhance efficiency with traceability systems, leading to a 30% reduction in production defects, resulting in considerable cost savings2.
This was the challenge that a multinational automotive and clean energy company faced in 2018, prompting a reevaluation of its processes to ensure 100% traceability and enhance customer satisfaction. Missing serial numbers on motors led to prolonged traceability processes for customers, causing production and delivery delays. Additionally, the uncertainty surrounding defective or broken parts resulted in time-consuming and costly replacements, escalating production costs for customers.
Unipart China aimed to revolutionise the company’s approach, guaranteeing complete traceability of every motor part. Our objective was to implement a streamlined process for tracking, detecting, and classifying motor parts, ultimately reducing costs and turnaround times for customers while increasing motor availability.